SMLC-15 Single Axis Motion Controller
ORMEC’s ServoWire Motion & Logic Controller (SMLC) is the center of a complete machine control solution to meet your motion, I/O and networking needs. This platform combines ORMEC's motion engine with high performance PLC capability and world class open standard software. Focus your engineering efforts on solving your application instead of integrating control components.
Key Features
SMLC Controllers
The SMLC-15 features high performance computing capability combined with a true real-time operating system (RTOS). Industry standard x86 32-bit processors run the QNX RTOS and provide cost effective, robust computing power for demanding single-axis motion and I/O control applications. SMLCs are used in a wide range of industrial and aerospace markets including packaging, converting, labeling, web & material handling, medical, pharmaceutical, as well as general assembly and winding.
Machine I/O
The SMLC-15 provides a multi-tiered, flexible approach to meet machine I/O requirements. It has the ability to interface high-speed drive-based I/O for microsecond position capture and single servo update response to sensor signals. Sub-millisecond programmable limit switch outputs are tightly coupled to the motion control.
General purpose I/O options are fully supported using WAGO 750 Series Ethernet I/O. A wide variety of cost effective analog and digital I/O modules are connected to and controlled by the SMLC.
ServoWire Drive Network
ORMEC’s AC brushless servo motors and ServoWire digital servo drives offer guaranteed performance with the SMLC. Maximum performance from a tightly integrated, pre-engineered package simplifies everything from system integration to maintenance.
Fully digital control offers compelling benefits—eliminating manual servo drive setup and providing real-time software access to all parameters. In an SMLC system, position, velocity and torque loops are closed by the digital signal processors (DSPs) in the ServoWire drives and are based on position commands sent from the SMLC. Velocity observer software eliminates the need for analog tachometers. Potentiometers are eliminated because gain and compensation parameters are set in software. All loop adjustments are automatically computed when a motor and its load inertia are specified in ServoWire Pro. This simplifies servo system tuning.
Using an SMLC-15 with XD drives
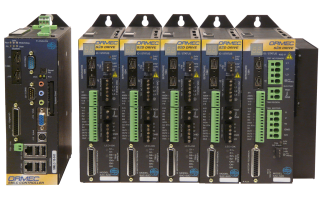
An SMLC-15 can be connected via Ethernet to up to 48 XD Indexers as a very cost effective solution to multi-axis systems that require limited synchronization between the axes. In this configuration, communication to the drives is done using Modbus/TCP function blocks. An application specific library for the SMLC simplifies this process for the user.
Specifications
General Specifications
- Input Voltage for AC model: 115/230 VAC 1.0/0.5A (+15%, -20%), 50/60 Hz, single phase
- Input Voltage for DC model: 24-48 VDC, +/- 10% (0.6A typical, 1.1A max @ 24VDC)
- Operating Temperature: 0 to 50C
- Relative Humidity: 10 to 95% @ 40C (non-condensing)
- Weight: Approx.3.1 lbs
- Dimensions: 9.0 x 2.75” x 7.2” (228.6 x 69.9 x 182.9 mm)
Processor & Memory
- Main Processor: Industry standard x86 32-bit processor
- DRAM: 128 Mbytes
- Program Memory: 128 Mbytes (Removable Compact Flash)
- Non-Volatile Memory: 32 Kbytes (battery backed)
Motion Control
- All-digital control algorithms featuring velocity and acceleration feedforward for optimal performance
- High-speed sensor inputs to initiate motion within one position command update
- High-speed hardware position capture (<1 usec), ideal for use in high-speed registration applications
- Software controlled position, speed and current (torque) limits
- Drive fault protection circuits, watchdog timers and integrated diagnostics for fail-safe operation
- Full 32-bit position count or modulo position in user units
Inputs/Outputs
- SMLC I/O: 8 inputs, 8 outputs, 1 analog in, 1 analog out.
- General I/O: 64 modules per WAGO 750 Series bus coupler, up to 512 I/O points connected via Ethernet (Modbus/TCP). Multiple bus couplers can be used for additional I/O.
Communications
- Standard: Two RS-232 serial ports
- Standard: Two Ethernet 10/100baseT ports with RJ45 connectors
- Standard Protocols: Modbus/RTU slave, Modbus/TCP client & server, Ethernet/IP adapter